Summary:The method of cam synchronizationWhen the embroidery machine is repaired, it is inevitable to encounter the cam synchron...
The method of cam synchronization
When the embroidery machine is repaired, it is inevitable to encounter the cam synchronously punching the table. How to correctly punch the table and determine the degree of hooking time is very important. The dial indicator is a high-precision measuring tool. It can only measure relative values, not absolute values. It is mainly used to detect the shape and position errors of the workpiece (such as roundness, flatness, verticality, runout, etc.) , its measurement accuracy is 0.01 mm. Simple, accurate and fast cam synchronous metering method: first align the pointer of the machine between 172º~173º on the dial (this step is more critical), and then wrap several layers of cloth on the main shaft, mainly to prevent the use of strong pliers Scratches on the surface of the spindle are caused. To align the degree, clamp the main shaft with strong pliers so that the main shaft cannot rotate, fix the position of the pliers, and then use a dial indicator to mark the bottom dead center of each machine head. Specific method: use the dial indicator measuring rod to hold the plastic body of the lower section of the drive block, turn the eccentric cam in the forward and reverse directions by hand, and repeatedly see that the dial indicator pointer points to the bottom dead center of the slider, tighten the eccentric cam tightly. Fix the screw, according to its method to adjust other head. Then adjust the encoder 100º position so that the hooking time degree is between 196º~198º. If the quilting machine is embroidering thick materials, the needle bar can be lowered to 200º, so that the needle skip phenomenon will not occur when most of the machine heads are hooked.
2. Maintenance of the thread trimming part
The thread trimming action angle of the embroidery machine is between 285º~286º, and some can set the thread trimming action angle and the thread trimming length hooking ratio. A simple method of adjusting the thread trimming cam is now introduced, which is the most commonly used method by the author when repairing the thread trimming part. When the machine stops at 100°, push the thread trimmer electromagnet up by hand, and the thread trimmer pendulum pin just enters the position where the arc of the thread trimmer cam groove is the lowest. This is the best position for the thread trimmer cam to be installed. Tighten the thread trimmer cam. The length of the thread trimming head can be controlled by a little movement of the screw and the thread trimming cam position forward and reverse. Note that when the thread trimming pendulum pin enters the thread trimming cam slot, there must be a gap left and right in the slot to prevent the pin from being stuck in the slot during thread trimming. The principle of embroidery electromagnet thread trimming mechanism is the same as that of computer lockstitch machine thread trimming mechanism. If it is found that some machine heads are not properly trimmed, you can check whether the position of the moving knife is too large, and whether the moving and fixed knife edges are worn. It is worth noting that the position of the thread trimming cam should not be changed under normal circumstances, and it can only be changed when most of the machine heads have poor thread trimming and overhaul.
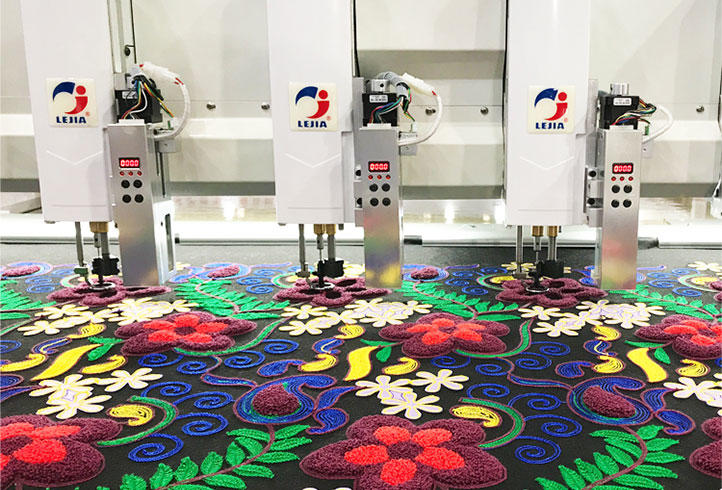
3. Causes and elimination methods of embroidery machine movement
Pattern "running flowers"
Press the pattern selection key on the operation panel to display the pattern and check whether the pattern is wrong.
Re-enter a pattern.
After the machine is turned off, check whether the embroidery frame is loose, whether the two sets of transmission belts in the X and Y directions are consistent, whether there is too loose or too tight, whether the pulley is tight, and whether foreign objects enter.
If it is not normal, repair the mechanical part.
Record the starting point data of the pattern and the position of the embroidery frame, and observe whether the pattern can return to the origin after "shifting". After moving, press "return to origin" or "starting point" key, the embroidery frame will return, and observe whether the starting point data on the screen is consistent with the recorded data.
If the data is inconsistent, the main control board is faulty.
Access the main control board section.
If the data are consistent, but the position of the origin of the frame is not correct, the stepping drive system is faulty.
Overhaul the stepper motor and driver and its transformer.
X or Y unidirectional movement
Check whether the connection cables of each part are faulty.
Troubleshoot the wiring and replace the faulty stepper driver.
Switch the stepper drivers in both directions and observe which driver is faulty.
Faulty drive power transformer or stepper motor.
Movement in both X or Y directions
The grid voltage is unstable and fluctuates too much.
Install a stable transformer.
The memory disk pattern is wrong.
After the system memory test, reset the data, and then input the pattern.
The step signal line is disturbed and caused to move.
Find the source of interference, check whether there is a DC voltage greater than 2 volts between the switching power supply (5V and 12V) and the rack, and if so, eliminate leakage.