Summary:
Skip stitch 1. The needle point of the machine needle is not sharp, and the hair is bent. Changing the needle2. The...
Skip stitch
1. The needle point of the machine needle is not sharp, and the hair is bent. Changing the needle
2. The gap between the needle and the hook tip is too large. Readjust the relative position of the hook
3. The tip of the hook becomes blunt or slightly defective. Grind and polish the tip of the shuttle
4. The embroidery stretch is too loose. Tight embroidered fabric
5. The pressure of the embroidery foot spring is insufficient or damaged. Replace the embroidery foot spring
6. The thickness of the embroidery thread does not match the needle. Choose the thickness of the needle according to the thickness of the embroidery thread.
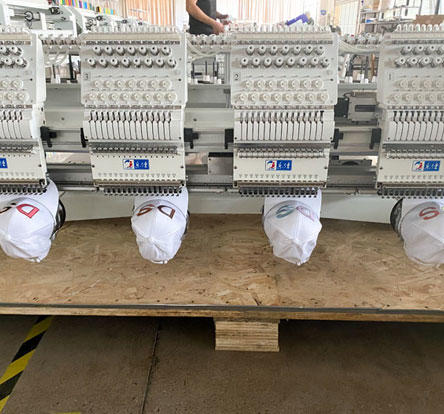
Disconnected
1. The tension of the bottom thread is too large. Just adjust the tension of the pressure plate and the bobbin to be even.
2. The needle hole has a quick cut. Change the needle
3. The thickness of the needle does not match the embroidery thread. Choose the thickness of the needle according to the thickness of the embroidery thread.
4. The hook tip is hairy. Polish the hook tip or change the hook
5. The upper thread is not lubricated, using silicone oil lubrication treatment
6. The hair of the shuttle makes the thread obstructed. Smooth or polish the hair.
7. Use sandpaper to polish the hair on the thread take-up rod hole
8. Tri-eyeliner hooks the hair with sandpaper to polish the hair
9. Polish the hair on the needle plate hole with sandpaper
10. The hair of the thread clamping plate and the thread clamping screw are polished with sandpaper
11. Position the hair and polish the hair with sandpaper
12. The gap between the positioning hook and the shuttle frame is unreasonable. Adjust the gap
13. The upper thread tensioner fails to clamp the thread. Remove the garbage in the tensioner
14. The direction of the needle groove is not correct. Adjust the direction of the needle groove so that the captain groove is aligned with the operator
Broken needle
1. The needle is bent, the tip of the needle is hairy, and the needle screw is loose. Change the needle and tighten the screw.
2. The hook is not properly matched with the needle. Adjust the position of the hook
3. The hook and needle fit too tightly. Adjust the position of the hook and needle.
4. The gear gap in the rotary hook box is too large. Re-adjust the gear gap.
5. The needle out cloth surface signal is inaccurate. Adjust the needle out cloth surface high and low position encoder position
6. The needles of the machine head are not synchronized. Adjust the needles of the machine head to enter and exit the cloth at the same time